Understanding The True Cost Of A Tyre Pyrolysis Plant
Purchasing a tyre pyrolysis plant will require you to invest in a number of important components. These components include the energy consumed, floor space needed, and condensers used. A high-quality plant will be able to produce an oil yield that is above average. A good condenser will also help reduce the cost of a tyre pyrolysis plant. Besides oil, steel wires and carbon black can also be sold directly.
Price of Tyre Pyrolysis Plant
The price of tyre pyrolysis plant depends on a variety of factors. The type of machine used and its capacity will have a large impact on the price. Continuous machines are generally more expensive, while progressive models are more cost-effective. The cost of a tyre recycling machine will also be higher if the device is designed to generate renewable energy without polluting the environment.
When determining the price of a pyrolysis plant, consider the installation space, labor, energy costs, and maintenance and repair costs. Also, choose the best model to meet your needs and budget. A pyrolysis plant should be designed to be safe, efficient, and able to serve you for a long time. It is also important to check the wire line to ensure it will work properly and to clean it after pyrolysis.
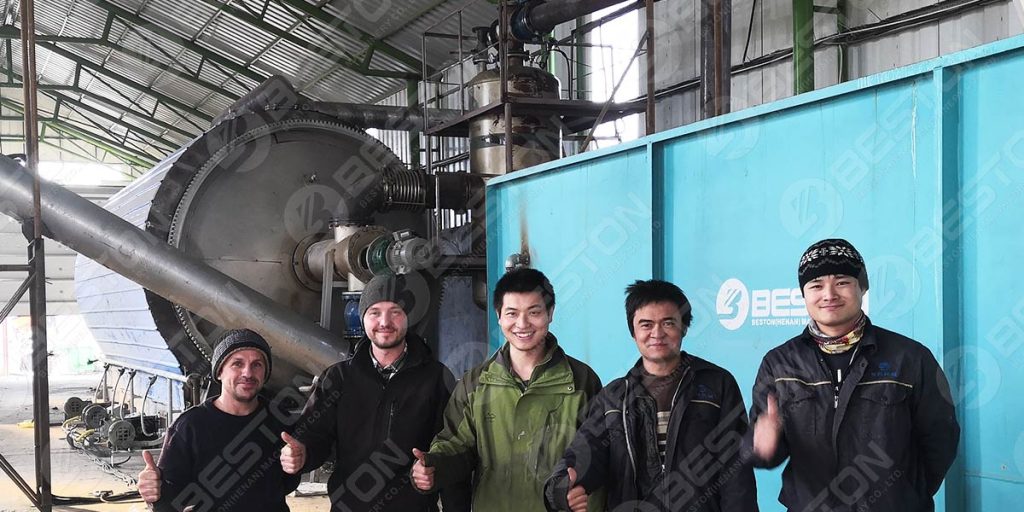
Energy Consumption
The pyrolysis of used tires is a sustainable alternative fuel technology that can produce renewable fuels from waste tires. It uses a process where carbon black and tire rubber are heated together. The result is a substance similar to diesel fuel and can be used in a compression-ignition engine.
The energy consumption of a tyre pyrolysis plant is measured in terms of the amount of fuel produced per kg of feedstock. The process produces approximately 6 MJ of energy for each kilogram of feedstock. The percentages of the pyrolysis products are given in Table 1.
The energy consumption of a tyre pyrolysis plant varies depending on the size of the plant. A 10 ton tyre pyrolysis plant uses around 20kw of electricity per hour. A 20-ton continuous tyre pyrolysis plant requires around 50kw of electricity per hour. Moreover, the process can last up to a month without a break.
Floor Space Required
A tyre pyrolysis plant is comprised of a series of components that process waste tyres into fuel. These parts include a tyre shredder, a feeding conveyor, a burning room, a heat exchange system, and a steel and carbon black separator and flue condenser. To start pyrolysis, the waste tyre should be broken into pieces that are between thirty and fifty millimetres in diameter.
A good fully continuous tyre pyrolysis plant should have a high heat resistance and tightness. In addition to processing tyres, this type of plant can also process other waste materials. Beston waste to energy equipment is an excellent choice for this purpose.
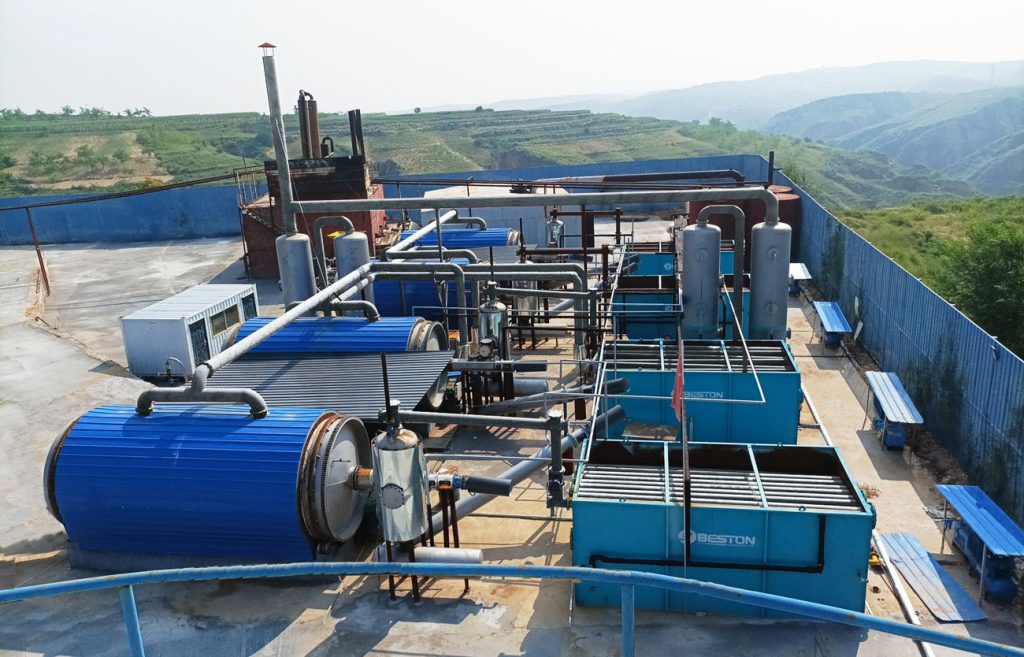
Condensers Used
A tyre pyrolysis plant uses condensers to collect the waste oil gas. The waste oil gas is a mixture of heavy oil gas and lighter oil gas. The heavy oil gas first has to cool down to a liquid before it can be discharged. The condenser used in this process prevents the oil sludge from collecting on the cooling pipe. This helps avoid gas jam problems.
In the waste tyre pyrolysis plant, a condenser is used to condense the waste gas into liquid. The waste gas contains methane, a common heating fuel. A condenser system is important in this process because it increases the amount of oil that can be condensed and the concentration of toluene, xylene, and pall rings.
Environmentally Friendly
A tyre pyrolysis plant produces weakly acidic wastewater. This wastewater is filtered through three stages to become harmless. It is then discharged into a dedicated evaporation processing unit using the flue heat from the main processor. After it passes through this process, it is ready for reuse.
A tyre pyrolysis plant is an energy efficient device that can recover oil and gas from tyres. This technology can reduce the dependency on oil and gas resources. In addition, it can promote circularity in the tyre industry. It can also help corporates meet their ESG goals.
The pyrolysis of old tyres can be a sustainable solution to the waste management problem. Currently, the natural decomposition of a tyre can take up to 150 years. However, this process is not environmentally friendly as it causes leaching of toxic organic compounds into the soil. Pyrolysis, on the other hand, is a process that produces no toxic waste. Moreover, the combustion products are non-toxic. Get tyre pyrolysis plant cost here.